Industry Trends: Critical Insights on the Current Automotive Semiconductor Shortage
April 02, 2021
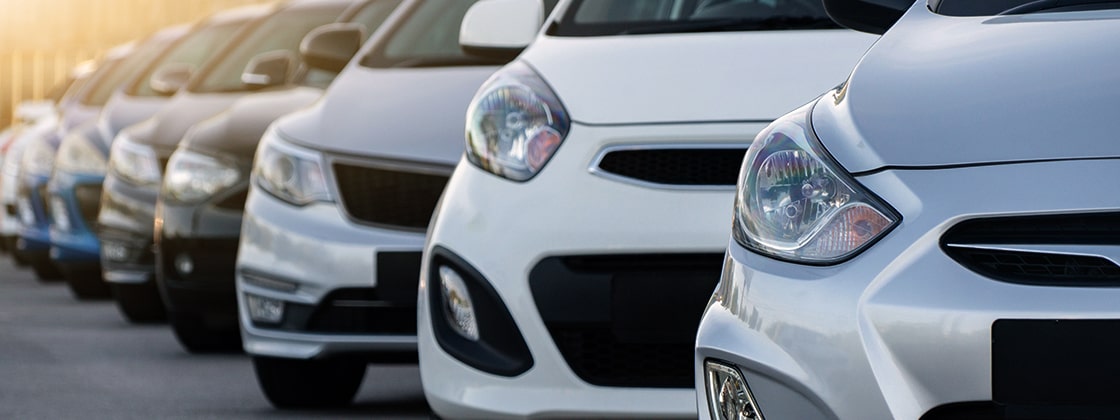
Guest Writer Mario Morales – Key Insights on the Automotive Semiconductor Shortage Industry Dynamics
No one could have foreseen that the world would face a worldwide pandemic in 2020. Supply chains were disrupted, first by lockdowns and manufacturing shutdowns, causing companies to pull in orders and build up inventory to reduce supply risk and maintain business continuity, and then by uneven demand and changing buying behavior from consumers. However, while some markets (e.g., automotive) are seeing shortages due to decisions made by OEMs, others are seeing tight supply, and some markets are working through excessive inventory accumulated in 2020 in areas around cloud infrastructure and memory. The situation today for most markets is not a story of excessive end-market system demand but rather a result of supply chain decisions made in 2020 that have limited capacity at certain process nodes.
Automotive Market
In the automotive market, 2020 was a year of drastic sales swings and manufacturing disruptions. OEMs faced sales declines, in some regions, of 40–50% y/y in the first few quarters of 2020 and then subsequent rebounds in the following quarter. OEMs remained unsure how sales would perform, given the trajectory of the pandemic, and supply and manufacturing disruptions due to lockdowns caused some automobile manufacturers to push out orders for parts, as they operate on a just-in-time philosophy. Semiconductors can take anywhere from six to eight weeks to manufacture, and foundries and integrated device manufacturers (IDMs) plan capacity up to a year in advance and adjust plans and reprioritize other products over months. When the automobile sales rebound was sustained through 4Q20 and OEMs recognized their semiconductor inventory issue in 4Q20, the impact was not one that could not be mitigated immediately.
Capacity Expansion
Beyond the disruptions caused by the pandemic, a contributing cause of the tight inventory and shortages can be traced back to decisions made two to three years ago when integrated device manufacturers and foundries were making capacity investment decisions. Most companies are not investing in expanding capacity at older process nodes and 200mm capacity, which are used for products for the automotive and industrial markets where specification and quality requirements are high and price sensitivity is stringent. By limiting capacity expansion, the semiconductor manufacturers reduced the amplitude of the swings of the semiconductor cycle. While this works in a steady growth scenario, it reduces the ability of companies to respond to sudden change. Foundries plan capacity up to a year in advance. Companies could not have anticipated the pandemic and its asynchronous impact on different industry sectors, but additional capacity could have lessened the situation companies face today.
Measures Taken by Semiconductor Companies
Automotive semiconductor manufacturers are reporting that they are in daily contact with automotive OEMs as they work to supply the industry. IDC believes this low-inventory environment will gradually be alleviated through the next couple of quarters as the supply chain is filled. The automotive semiconductor market will rebound in 2021 compared with 2020 despite these short-term inventory shortages. Other semiconductor categories such as power management integrated circuits (PMICs), some sensors, and display drivers were also impacted by a pull in of orders by semiconductor customers. Capacity should increase gradually as dedicated foundries add additional wafer starts.
IDMs and foundries are increasing wafer starts to address the supply issues, and TSMC is expediting automotive chip production. Conditions should improve gradually, and these issues should be mitigated by 3Q21, unless another shock to the market occurs. The impact of COVID-19 variants is still unknown and could add additional uncertainty into the market.
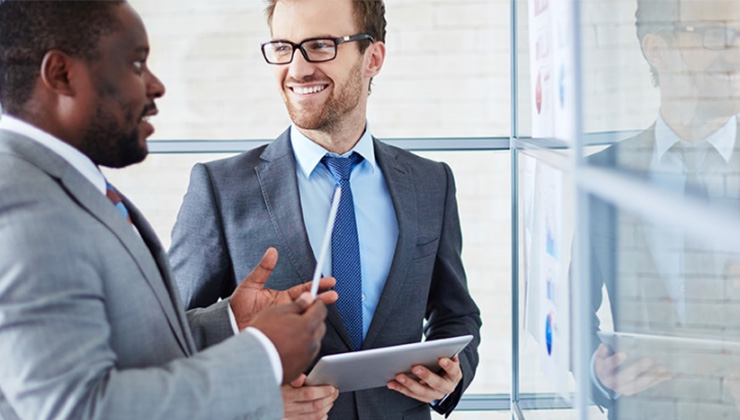
Advice for the Technology Supplier and Technology Buyer
Technology Supplier
IDC offers the following points of guidance for IDMs and foundries:
- Rationalize inventory and customer orders to avoid double orders and watch for potential oversupply. Validate that end-system demand is real. This will be important to decrease the amplitude of the next semiconductor downturn cycle.
- Consider diversification of manufacturing (location and supplier). Longer term, semiconductor manufacturing diversification (company and/or geographical location), as well as an increase in investment in semiconductor manufacturing capacity, should be a priority to enable a more flexible response. The Texas power outages, recent earthquake and fire disruptions highlight factors that semiconductor manufacturers must consider beyond employee costs and tax breaks when determining manufacturing sites and partnerships with the supply chain.
Technology Buyer
IDC offers the following points of guidance for companies purchasing semiconductors or semiconductor companies utilizing foundries:
- Have closer planning with suppliers. OEMs dependent on a secure semiconductor supply should closely work with their suppliers to factor in manufacturing lead times or potential disruptions in conjunction with their own manufacturing plans. Transparency across the supply chain enables supply risk management and delivers efficiencies for both customer and supplier.
- Extend supply risk management down. Supply risk management can be improved by understanding the supply chain a few levels down and working with technology suppliers to identify potential bottlenecks or single source risks and execute on a collaborative business continuity plan.
- Develop industry-specific supply chain management strategies and mitigation plans. The myriad parts necessary for manufacturing are impacted by different factors. Having industry risk–aware supply chain plans can potentially mitigate unusual conditions when they arise in a particular market.