Tariffs update: The impact on fleet operators
May 01, 2025
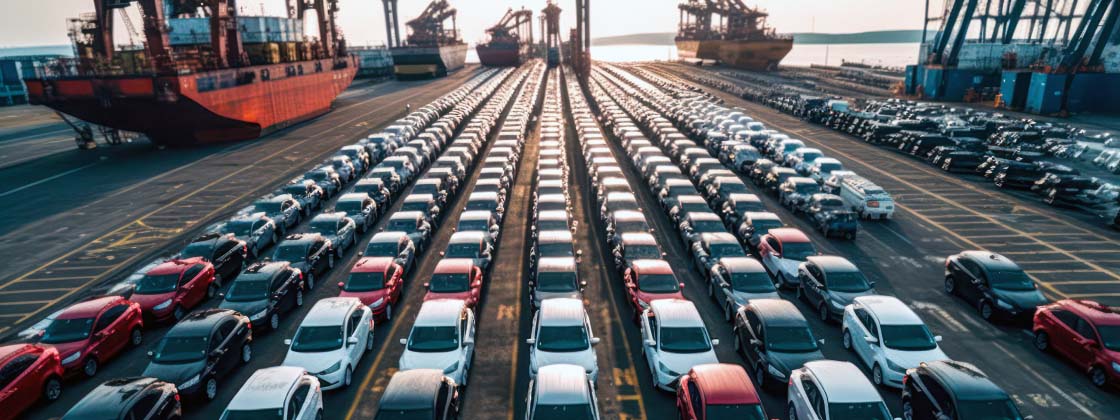
Element Senior Vice President, Strategic Advisory & Analytics, Steve Jastrow, offers insights and recommendations for fleet managers as they adapt to the latest tariff changes.
One of the biggest challenges fleet managers and business leaders are navigating is the evolving impact of automotive-related tariffs.
From supply chain adjustments to maintenance planning, these tariffs continue to affect the fleet industry in multiple ways. While some clarity has emerged with recent updates, including the elimination of stacking tariffs and the introduction of the temporary "import adjustment" rebate, questions still remain about the long-term effects and how fleet operators can best respond.
To provide a clearer understanding of these impacts, we sat down with Element’s Senior Vice President of Advisory & Analytics, Steve Jastrow. He offers invaluable insights into how tariffs will shape fleet operations, actionable strategies to minimize disruption, and recommendations for navigating the new tariff landscape with confidence.
Steve, there are multiple tariffs in play. Could you please give us a summary of the tariffs that will affect the fleet industry?
The three main tariffs currently impacting the fleet industry are:
- Tariff on imported vehicles – The U.S. administration has imposed a 25% tariff on cars and car parts not built within the U.S. With the recent changes, the elimination of stacking tariffs means only non-U.S. content within vehicles will be subject to this tariff, significantly altering the cost calculation compared to previous rules.
Under the United States-Mexico-Canada (USMCA) Agreement, automobile parts compliant with USMCA guidelines will remain tariff-free. Any non-USMCA content within these vehicles, however, will face a 25% tariff. Current protocols allow importers to certify their U.S. content accordingly. This tariff is expected to remain in place for the foreseeable future. - The Canada/Mexico tariff – While a final decision on this tariff for vehicles from Canada and Mexico is still pending, it appears the likelihood of an additional tariff on these countries has decreased under the adjusted trade policies. If such a tariff is introduced, only non-USMCA content might face additional tariffs, avoiding the previously compounded effects. For now, no new multi-layered tariffs are expected, but this remains an area to watch.
- The tariff on steel and aluminum – The 25% tariff on steel and aluminum remains unchanged and continues to be a significant factor for fleet managers. However, the elimination of stacking tariffs offers some relief when these materials are incorporated into U.S.-built or USMCA-compliant vehicles. This tariff is expected to stay in effect for an extended period.
These recent adjustments, including the introduction of the "import adjustment" rebate for U.S.-built vehicles using imported parts, signal a shift in how tariffs are structured to provide selective relief. While this rebate mainly benefits original equipment manufacturers (OEMs), fleet managers may see indirect benefits through reduced cost burdens on certain vehicle components.
How do the upcoming tariffs affect fleet acquisition costs, particularly for vehicles and parts sourced from outside the country?
SJ: It’s crucial to begin by understanding the significance of the recent tariff updates. The elimination of stacking tariffs is one of the most impactful changes. Previously, tariffs could be compounded, with non-USMCA content facing repeated tariffs during production and upon completion. With this adjustment, only non-USMCA content will incur a single 25% tariff, reducing the overall cost burden compared to previous rules. Vehicles compliant with USMCA guidelines remain tariff-free for their U.S., Canadian, or Mexican content.
The changes to President Trump’s 25% vehicle tariffs will provide auto companies with credits for up to 15% of the value of vehicles assembled domestically, making 15% “tax-free”, which equates to a 3.5% reduction in the tariff. This adjustment has allowed automakers to better structure costs for vehicles built in the U.S. or with higher domestic content, which is reflected in the accompanying scenario. To provide a clearer picture, here’s an example of the math under the revised rules:
Scenario |
Tariff Impact |
---|---|
If a car is built in the U.S. with 85% U.S. or USMCA content |
The manufacturer will effectively avoid tariffs on vehicle production for the first year |
If a vehicle is built in the U.S. with 50% U.S. or USMCA content and 50% imported parts |
The manufacturer only pays the 25% tariff on 35% of the imported componentry, rather than the full 50% |
For vehicles manufactured outside the USMCA region, there’s still a 25% tariff applied to non-U.S. content, which is likely to remain in place. However, the ability to certify U.S. content should provide importers and OEMs with some flexibility. It’s also worth noting that while costs for these vehicles increase, the more streamlined application of tariffs may simplify calculations and reduce pricing volatility.
A notable development is the "import adjustment" rebate now available for U.S.-built vehicles that use mostly U.S. or USMCA parts. The import adjustment applies here, providing temporary benefits for pricing stability. Paying attention to such shifts is critical for operators looking to manage costs effectively.
For fleet operators, the lessons learned from recent supply chain disruptions remain relevant. Prioritize vehicles with higher U.S. content to reduce tariff impacts, diversify OEM agreements, and maintain flexibility to adapt to evolving conditions. Additionally, monitor price protection agreements closely, as OEMs are adjusting their policies, with some already scaling back coverage. For example, Ford and Stellantis have announced expiration dates on price protection, while GM has extended protection on certain models. These agreements could change further in upcoming model years, making it more important than ever to place orders promptly to lock in pricing.
From a Canadian perspective, tariffs on U.S.-made vehicles remain in place, but auto parts appear to be excluded. Canadian fleet leaders should continue to emphasize USMCA-compliant models, place orders early, and diversify their OEM partnerships. Stay informed, as the situation can shift quickly and have downstream effects on procurement and costs.
Ultimately, the key is to maintain flexibility and adaptability, ensuring your fleet strategy stays aligned with these rapidly evolving trade policies.
What measures can fleet operators take to minimize delays caused by global supply chain challenges and tariff updates?
SJ: The fragility of global supply chains continues to be a concern, but there are proactive steps fleet operators can take to reduce delays, especially with the recent tariff changes.
While the elimination of stacking tariffs simplifies cost calculations and provides some relief, new challenges may arise if OEMs pivot to sourcing parts outside the USMCA region or adjust operations due to the tariffs. Disruptions may not reach the severity of those experienced during COVID-19, but extended delivery times and potential order bank closures are still risks to consider.
To minimize these delays, I recommend placing vehicle orders as early as possible to reduce bottlenecks and secure your position in OEM production schedules. Focus on sourcing vehicles with significant U.S. or USMCA content to reduce exposure to tariff changes. This approach can limit the impact of the 25% tariff on non-USMCA components while benefiting from the "import adjustment" rebate where applicable.
Another priority should be replacement planning if you’re operating an older fleet. Target high-mileage vehicles or those with the highest operational impact for replacement first. Delaying replacements risks increased downtime and unexpected costs.
Lastly, diversify your OEM agreements. The lessons of recent years have shown the dangers of relying too heavily on one supplier. Establishing relationships with multiple OEMs ensures flexibility and access if supply chain disruptions occur. Remember, it’s not just about where the OEM is headquartered but where the vehicles and their components are produced.
What impact will these tariffs have on the overall operational expenses of fleet companies, including things like fuel and maintenance?
SJ: Operational expenses are expected to rise, even with the elimination of stacking tariffs, as many cost pressures remain. Maintenance costs in the U.S. may increase as parts sourced from Mexico or Canada face higher prices due to the tariffs. OEMs may shift to sourcing components domestically, which could cause delays in acquiring parts, leading to extended vehicle downtimes that lower fleet utilization.
Fuel costs also remain a concern. Since USMCA protections exempt fuel imports from Canada from tariffs, oil prices could still fluctuate due to external factors like geopolitical tensions or production adjustments by OPEC. Currently, fuel prices are lower due to fears of an economic slowdown coupled with increases in oil production. However, even small increases in fuel costs can significantly affect fleet budgets.
Insurance premiums will likely rise as well since the higher costs of vehicles and parts will drive up repair and replacement expenses.
Fleet operators should focus on optimizing preventive maintenance schedules to reduce downtime and avoid costly repairs. A proactive risk management strategy can also help you lower your total cost of risk. Strategic planning here will help offset some of these rising expenses.
What financial strategies should fleet leaders in both the U.S. and Canada adopt to hedge against tariff-related cost increases?
SJ: Financial preparedness is key. The first step is to work alongside your finance team to reflect tariff-related price increases in vehicle acquisition budgets. Start treating certain tariffs, like the ones on steel and aluminum, as fixed costs rather than temporary spikes. For instance, the 25% tariff on non-USMCA content should now be treated as a long-term cost rather than a short-term spike.
Avoid delaying replacement cycles unless absolutely necessary. While the "import adjustment" rebate provides temporary relief for vehicles with U.S. content, its benefits primarily go to OEMs and will phase out in the coming years. A slight cost increase now may save more in the long run, especially considering the potential costs from aging fleets or reliance on rental vehicles.
Use analytics to prioritize vehicle replacements. Focus on high-priority or high-mileage vehicles first to maintain operational efficiency. At the same time, explore opportunities for route optimization and fuel efficiency to further reduce operational costs. You can allocate resources more effectively by honing in on what is critical to your operations.
What are your top three recommendations for fleet managers today?
-
Prioritize domestically built alternatives: With shifting tariffs and international trade policies, prioritizing vehicles manufactured predominantly locally can help organizations reduce their exposure to unexpected costs. By focusing on domestic alternatives, companies can avoid tariff-related price hikes and ensure more predictable budgeting for fleet procurement.
For U.S. operations, it’s also important to understand the total cost of ownership of your vehicle options. Domestic models may still be significantly impacted by the tariffs if their parts are sourced outside of the U.S./USMCA region.
On top of the vehicle’s price, things like OEM concessions and price protection agreements will help determine which vehicle option is most suitable for your fleet.
Collaborate closely with your fleet advisors to assess your pricing options as well as your current lineup. They can also help identify domestic makes and models that meet your operational needs, such as vehicle capacity, fuel efficiency, or specialized features.
-
Stay on schedule with replacements: Delaying fleet replacements might seem like a cost-saving measure in the short term, but it often leads to long-term challenges (we are still digging out from the last supply chain crisis). Older vehicles are more prone to breakdowns, resulting in higher maintenance costs, unplanned repairs, and increased downtime, which impacts productivity.
Additionally, aging fleets consume more fuel and may not meet newer efficiency or emissions standards, further driving up operational costs. Sticking to planned replacement cycles ensures that your fleet remains reliable, efficient, and cost-effective. Regular vehicle updates also mean access to the latest technology and safety features, enhancing overall performance and reducing operational risks.
-
Stay informed: Things are changing and they're changing quickly, without a lot of warning. So, for our clients, I suggest you check in with your advisor, your account manager, and your FPS partner to find out the latest. If we don't have the answer at our fingertips, we'll figure it out and get back to you.
For those navigating this on their own, we have an open portal on our website where we compile the latest events along with some recommendations. Ultimately, staying informed empowers your team to adapt, navigate challenges, and stay prepared for whatever may come.
Successfully navigating the uncertainties created by these tariffs requires clear-eyed planning and decisive actions. Contact us to learn how we can guide you through these challenging times.
Never miss an update
Subscribe for more news and thought leadership from Element.