How do tariffs affect fleet collision repairs?
May 22, 2025
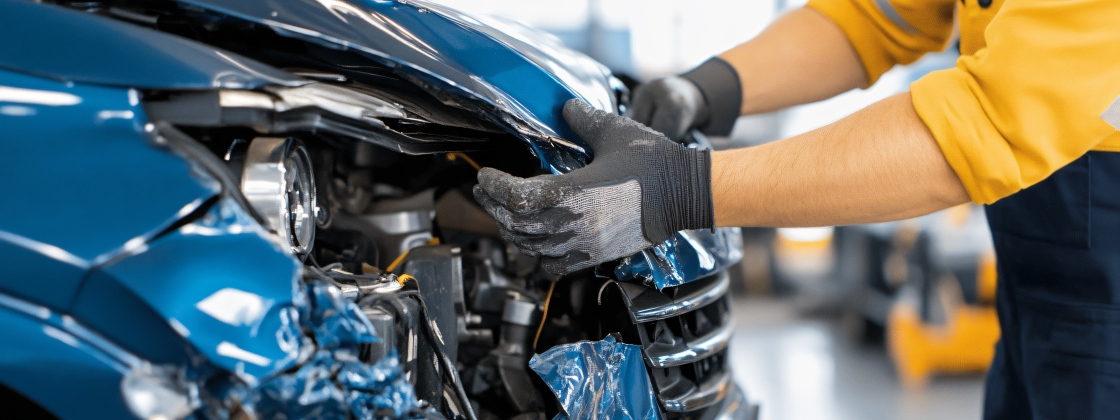
Tariffs on collision repairs might just seem like another industry expense, but they can actually have a broader and deeper impact than you’d think.
We’ve been looking into the data, and here are three key things every fleet manager should know about how tariffs could affect repair costs and timelines.
-
Average repair costs are expected to increase by $125–$150 per claim, based on a 2.5% total rise on a typical $6,000 repair.
-
Estimated fleet repair timelines will stretch by 20–25% due to supply chain bottlenecks and the availability of key components.
-
The impact will not be immediate but instead will increase over time as inventories of parts and materials deplete.
This means big changes across the industry, potentially impacting everything from repair schedules to fleet downtime. In this post, we’ll take a closer look at how tariffs are shaking things up in three key areas of collision repair: parts, materials, and tools (plus labor).
How do tariffs affect auto parts?
Parts are at the core of collision repairs, and tariffs introduce challenges that work their way through the supply chain in three major areas:
-
Original equipment manufacturer (OEM) parts: Increase expected at 15%
OEM parts like body panels and headlights are getting costlier, and tariffs on steel, aluminum, and microchips are a big reason why. Since most microchips come from China, these tariffs are causing costs to spike almost instantly.
Manufacturers are trying to work around this by shifting production to new suppliers in more cost-friendly geographies, but that's easier said than done. Smaller parts can be switched over in a few weeks. But bigger components like body panels take 6–8 weeks to retool and set up elsewhere.
So, what does this mean for you? Higher prices now and possible delays down the road. It’s a tough situation, but one to keep an eye on if you rely on OEM parts.
-
Aftermarket parts: Increase expected at 15%
Aftermarket parts, often sourced from China and India, are taking a big hit from tariffs on raw materials and electronic components. While they’re usually a budget-friendly alternative to OEM parts, their availability can be unreliable, especially during tough market conditions like these.
Once inventories run low, restocking cycles kick into gear, and that’s when prices start climbing as batch production struggles to keep up with demand. You may start seeing major shortages in aftermarket parts, leaving businesses scrambling to find alternatives. It’s a challenge no one wants, but it’s the reality we’re heading toward.
-
Like-kind-and-quality (LKQ) parts: Increase expected at 25%
LKQ parts (recycled or used car parts from salvaged vehicles) are usually a great budget-friendly option. But tariffs are changing the equation in an unexpected way. As resale values climb, fewer vehicles are being labeled as "unrepairable" and sent to the salvage yard.
With fewer salvaged cars available, the cost of LKQ parts is going up. Complicating the issue is the fact that sellers are repricing these parts daily, adjusting quickly to shortages. So, if you’ve noticed prices climbing already, brace yourself—steeper hikes (think 25% or more) could be around the corner, especially as OEM and aftermarket supplies tighten.
What is the tariff impact on materials used in collision repairs?
Repair costs are going up, and it’s affecting materials like paint, coatings, fasteners, and even everyday items like abrasives and welding parts. The price for these materials has increased by an average of 20%. So, why is this most concerning for fleet managers?
Collision repairs rely on high-quality materials to make sure vehicles are safe and functional after fixes. Take abrasives, for example—they’re essential for grinding and cutting, but tariffs on raw materials like steel are driving up production costs. And let’s not forget paint and coatings, which often lean on imported chemicals that are also getting more expensive.
At first, these price hikes might seem small, but for larger fleets, the costs add up fast. If these increases stick around, repair budgets could end up significantly higher than expected. It’s definitely something to keep an eye on.
Why tools and labor will likely become more expensive
The tools and equipment used in fleet collision repairs aren't immune to rising costs, especially with tariffs in play. High-tech gear like frame measuring systems, welding equipment, and calibration tools often rely on electronic components, which are getting more expensive because of tariffs on microchips and other manufactured goods.
While tools are built to last and price changes take time to show up, they eventually impact labour rates. Shop owners must factor in these higher costs when setting rates, which could jump by 15–25%. We saw how quickly labour costs climbed during the COVID-era supply chain crunch, and tariffs could trigger a similar long-term effect.
Delays may outlast the price hikes
Rising costs are frustrating, but what’s even worse is how repair cycles are slowing down. Parts shortages caused by tariffs mean longer repair times for everyone so expect downtime to jump by 20–25%.
Here’s a scenario we’re likely to see more often: A non-drivable fleet vehicle sits untouched for weeks because the parts needed are either backordered or unavailable. In cases like this, we’d have to ask—does it make more sense to salvage the vehicle instead of waiting? These days, deciding whether a car can be repaired isn’t just about cost, but also about logistics and liability.
Supply chain disruptions tend to follow a pattern:
-
3–4 weeks after tariffs hit: OEM parts start becoming harder to find.
-
6–8 weeks in: OEM part shortages get worse, and even aftermarket and LKQ inventories start running low.
The good news? If you start preparing in advance, you can reduce the impact of these delays on your fleet operations. Planning ahead makes all the difference!
Preparation is key
Tariffs will make their presence felt in the fleet collision repair world, affecting everything from parts and materials to labor costs and repair timelines. For fleet managers and business leaders, staying ahead of these challenges is more important than ever.
Need help navigating it all? Our team of trusted experts is here for you. Whether it’s planning fleet repairs, reducing downtime, or keeping costs in check, we’ve got your back.
Never miss an update
Subscribe for more news and thought leadership from Element.